Lessons Learned (LeLe) in the context of FMEA
1. Challenge / Task (Why)
Day-to-day business is often dominated by quick problem-solving (firefighting). This poses the risk that improvements for future or parallel applications with similar issues are not systematically developed and implemented.
2. Objective of this article
The article shows organizational and methodological approaches to realizing sustainable Lessons Learned processes.
3. What and How
The starting impulse for LeLe processes are the 8 Disciplines (8D) or identified improvement potentials in day-to-day business. Particularly relevant are the disciplines D2, D4, D5, and D6.
The results of LeLe are authorized instructions for action within a company. It is necessary to define organizational units and responsibilities that are responsible for the LeLe process. LeLe only work through active sponsorships as well as authorization and budget authority. Otherwise, short-term goals dominate, which in the worst case can block sustainable LeLe activities. In this context, it must be ensured that LeLe transfers to other projects or product groups work.
A Centre of Competence (CoC) is proposed, which is responsible, among other things, for the implementation or rejection of specific LeLe contents. The core point is the competence to authorize LeLe.
FMEA Templates
In the context of FMEA, it is necessary to update FMEA templates based on LeLe. This ensures that LeLe contents are available for future FMEAs. This can, for example, concern:
- Types of failures
- Consequences of failures
- Prevention controls with adjusted O values
- Detection controls with adjusted D values
4. Result
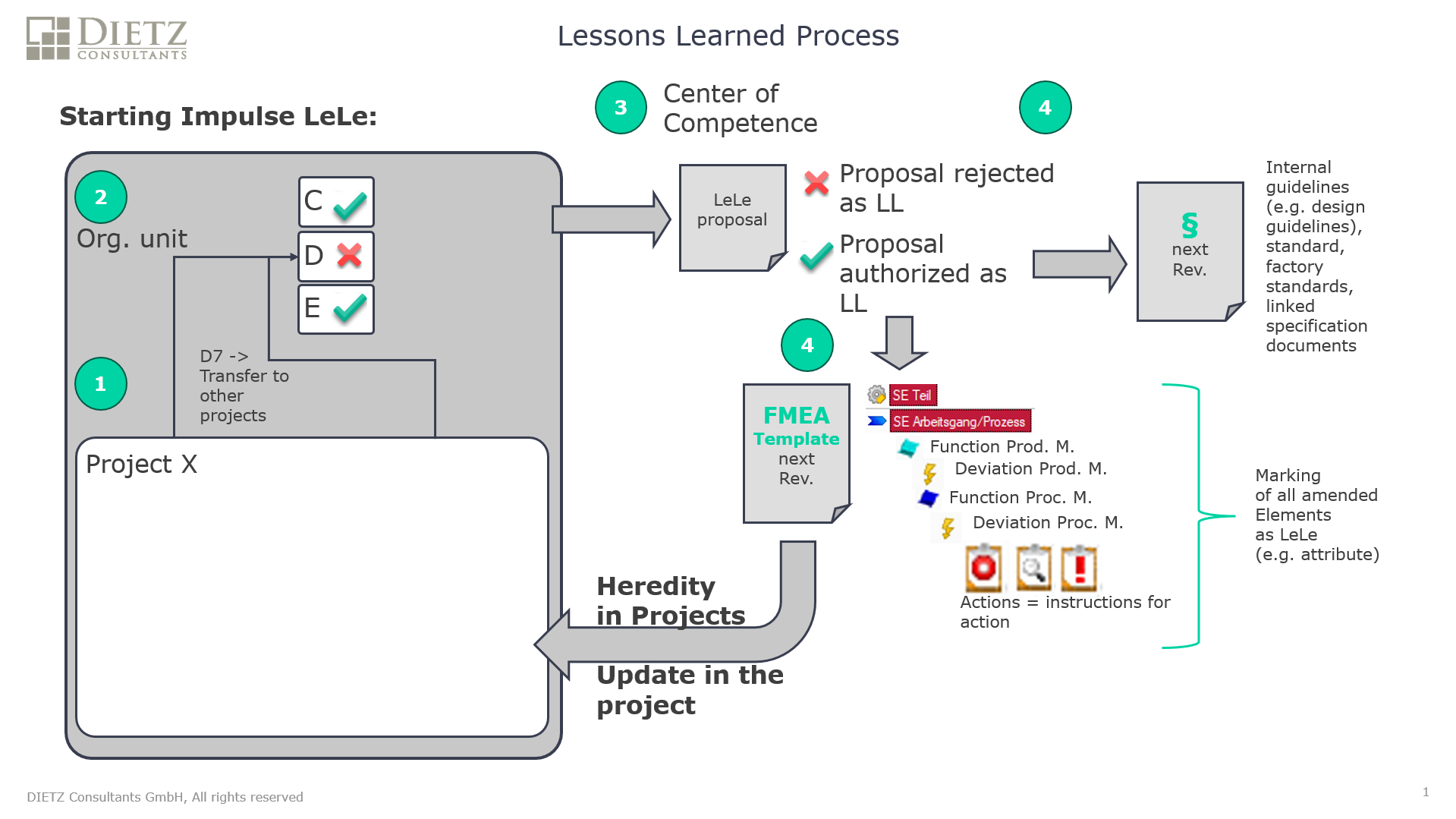
Through LeLe, regulations and guidelines gain the ability to adapt. This is an important aspect of shaping future viability. On the meta-level, this concerns, for example, the constitutions of states that are adaptable. In contrast, religious rules that cannot be adapted are doomed to eventually fall out of time.